We are committed to providing the best support for all our customers, regardless of their experience level. If you come across any unfamiliar terms while exploring our website, don't worry! We've got you covered with our handy glossary below. It contains definitions for all the technical jargon and terms, ensuring a smooth and clear understanding of our products and services.
Andon
Andon is an essential system in manufacturing that allows workers to promptly alert team members and management about quality or process issues. This is typically achieved by activating a light on a signboard that specifies which workstation has either observed a quality issue or is facing operational difficulties. In digital factories this is often done with dashboards.
The term Andon originates from Japan, and its meaning is roughly translated as "lantern." This is because the system functions like a lantern, highlighting issues on the production line as soon as workers detect them. By doing so, companies can quickly respond to problems and frequently pursue continuous improvement. Andon is crucial for ensuring quality control and promoting operational efficiency in manufacturing.
Application Programming Interface (API)
An API, or Application Programming Interface, is a set of protocols, routines, and tools for building software applications. It specifies how software components should interact and communicate with each other, allowing different systems or applications to share data and functionality. Essentially, an API acts as an intermediary between two applications, allowing them to communicate and interact with each other.
Batch
A batch refers to a specific quantity of a product that is produced in a single production run. The size of a batch can vary depending on the product being manufactured and the equipment used. For example, in the pharmaceutical industry, a batch may refer to a specific quantity of a medication produced using the same equipment and processes, with the goal of ensuring consistency and quality control. Batch production is often used in contrast to continuous production, which involves the ongoing production of a product without interruption or the need to stop and start production runs.
Bill of Materials (BOM)
A bill of materials (BOM) is a comprehensive list of all the raw materials, components, and sub-assemblies needed to manufacture a finished product. It includes all the information required to purchase, produce, and assemble the required parts, such as item names, descriptions, part numbers, quantities, and unit of measure. The BOM is an essential document for the manufacturing process, as it provides a detailed plan for the procurement and assembly of components, ensuring that the finished product is manufactured correctly and to the required specifications.
Cross-Training
Cross-training is the practice of training employees in multiple job roles or functions within an organization. It is a process of teaching an employee additional skills, knowledge, and competencies beyond their current job description or position. The purpose of cross-training is to increase the flexibility of the workforce, improve employee morale, reduce the risk of a single point of failure, and provide career development opportunities to employees. By cross-training employees, they can take on new roles during absences or peak production periods, which can ultimately lead to increased productivity and efficiency.
Cycle Time
Cycle time refers to the total amount of time it takes to complete a single production cycle or process, from start to finish. It includes all the steps involved in the process, including processing, waiting, inspection, and transportation times. It is often used as a performance metric in manufacturing to assess the efficiency of a production process and identify areas where improvements can be made to increase output and reduce costs.
Digital Twin
A digital twin is a virtual replica of a physical object, system, or process that is used to simulate, monitor, analyze, and optimize its real-world counterpart. Digital twins are created by combining data from sensors, machines, and other sources to create a virtual model that can be used to simulate the behavior of the physical object or process in a digital environment. This enables users to analyze and optimize the performance of the physical object or process in real-time, and to predict and prevent potential issues before they occur. Digital twins are used in a wide range of industries, including manufacturing, healthcare, and transportation.
Downtime
Downtime refers to the period of time when a machine or equipment is not operational or not performing its intended function. Downtime can be planned or unplanned, and it can result from various causes, including maintenance, repair, tooling changes, material shortages, and equipment failure. Downtime can have a significant impact on productivity, production schedules, and delivery timelines. Reducing downtime is a key goal of many manufacturing companies, as it can help improve efficiency, reduce costs, and increase profitability.
Enterprise Resource Planning (ERP)
An ERP is a type of business management software that allows organizations to manage and automate their core business processes in real-time. ERP systems integrate various departments and functions, such as finance, human resources, procurement, inventory management, and customer relationship management, into a single unified system. This helps organizations to streamline their operations, improve productivity, reduce costs, and enhance decision-making capabilities.
Gap Analysis
Gap analysis is a technique used to identify the difference or gap between the current state and the desired or expected state of a business or organization. It is often used as a tool for organizational change or improvement by identifying areas where a company is falling short of its goals or standards. Gap analysis involves comparing current business processes, performance metrics, and strategies to the desired future state, and then identifying what needs to be done to bridge the gap.
High-Mix Low-Volume (HMLV)
High-mix low-volume (HMLV) refers to a manufacturing production process that produces a wide range of customized products in low volumes. HMLV manufacturing is often used to produce a range of different products to meet the varied needs of customers, rather than producing a large volume of a single standardized product. This type of manufacturing can be more complex and costly than producing a single product in high volume, but it allows companies to offer a broader range of products and respond more quickly to changing customer demands.
Internet of Things (IoT)
The Internet of Things (IoT) refers to a network of physical objects, devices, vehicles, buildings, and other items that are embedded with sensors, software, and network connectivity, allowing them to collect and exchange data with each other and with other computer systems over the internet. This enables the objects to be monitored, controlled, and optimized in real-time, creating new opportunities for automation, efficiency, and innovation in a wide range of industries, including manufacturing, transportation, healthcare, and more.
Just-in-Time (JIT)
Just-in-time (JIT) is a manufacturing philosophy that aims to produce and deliver products just in time to meet customer demand, with minimal inventory on hand. JIT systems strive to improve efficiency and reduce waste by streamlining the production process, minimizing inventory holding costs, and improving overall quality. JIT systems typically rely on close collaboration between suppliers and manufacturers to ensure that raw materials and parts are delivered exactly when needed, and in the required quantities, to support a continuous production flow.
Key Performance Indicator (KPI)
Key performance indicator (KPI) is a measurable value that demonstrates how effectively a company is achieving its key business objectives. KPIs are used to evaluate the success of an organization or of a particular activity in which it engages. Examples of KPIs might include financial metrics such as revenue growth, profit margins, or return on investment, or operational metrics such as customer satisfaction, on-time delivery, or defect rates. KPIs can help businesses identify areas of improvement, make informed decisions, and track progress over time.
Lead Time
In manufacturing and supply chain management, lead time refers to the time it takes to fulfill a customer order or to procure raw materials, components or subassemblies needed for production. It encompasses the entire process from placing an order, to processing it, to manufacturing and finally delivering the product. Lead time can vary depending on factors such as the complexity of the product, the availability of raw materials, the manufacturing process, and transportation times. Shorter lead times can lead to higher customer satisfaction and increased operational efficiency.
Lean Manufacturing
Lean manufacturing is a methodology that aims to reduce waste and increase efficiency in manufacturing processes. It originated in Japan and is also known as the Toyota Production System. The focus of lean manufacturing is to eliminate any steps or activities that do not add value to the final product or service, known as waste. This includes overproduction, waiting, excess inventory, unnecessary transportation, overprocessing, defects, and unused employee creativity. By reducing waste and focusing on continuous improvement, lean manufacturing aims to increase efficiency, reduce costs, and improve product quality.
Manufacturing Execution System (MES)
A Manufacturing Execution System (MES) is a computerized system that is used in manufacturing to manage and monitor work on the factory floor. It provides real-time data on the production process, allowing manufacturers to monitor and control production in real-time. MES software can track machine downtime, production rates, and other critical factors to help managers make informed decisions. It can also provide detailed production reports and analytics to help manufacturers identify areas for improvement and optimize production processes.
Overall Equipment Effectiveness (OEE)
Overall Equipment Effectiveness (OEE) is a metric used in manufacturing to measure the efficiency and productivity of equipment and machinery. It is calculated by multiplying the availability, performance, and quality rates of the equipment. The availability rate measures the percentage of time that the equipment is available for use, the performance rate measures the speed of the equipment, and the quality rate measures the percentage of products produced that meet the required quality standards. OEE is used to identify areas for improvement in the production process and to increase the productivity of the equipment.
Pareto
Pareto, also known as the 80/20 rule or the Pareto Principle, is a concept in economics and business management that states roughly 80% of effects come from 20% of causes. It suggests that a small number of factors have a disproportionate impact on outcomes. The principle is named after Italian economist Vilfredo Pareto, who observed that 80% of Italy's land was owned by 20% of the population. The Pareto principle has been applied to a variety of fields, including manufacturing, quality control, and project management.
Poka-Yoke
Poka-yoke is a Japanese term used in manufacturing that means "mistake-proofing" or "error-proofing". It refers to any mechanism or technique used to prevent errors or mistakes from occurring in a production process. The goal of poka-yoke is to eliminate defects by preventing, correcting or drawing attention to human errors as they occur. This can include simple physical devices or more complex systems and procedures that detect and prevent errors from happening. The aim of poka-yoke is to improve product quality and reduce waste, defects and costs in manufacturing processes.
Root Cause Analysis (RCA)
Root Cause Analysis (RCA) is a problem-solving technique that is used to identify the underlying cause of a problem or incident, rather than just treating the symptoms. The goal of RCA is to find the root cause of a problem so that it can be effectively addressed and prevented from recurring in the future. The process involves investigating the event, gathering data, analyzing the data, identifying the cause, and implementing corrective actions. RCA is commonly used in various industries, including manufacturing, healthcare, and information technology.
Six Sigma
Six Sigma is a data-driven methodology and philosophy for achieving quality improvement in any process, product, or service. It involves the use of statistical methods and tools to identify and eliminate defects and minimize variability in processes. The goal of Six Sigma is to achieve a process that produces outputs with no more than 3.4 defects per million opportunities (DPMO). The methodology is organized into five phases: Define, Measure, Analyze, Improve, and Control (DMAIC) and it is widely used in industries such as manufacturing, healthcare, and finance.
Software as a Service (SaaS)
Software as a Service (SaaS) is a software delivery model in which the software application is hosted by a third-party provider and made available to customers over the internet. In this model, users typically pay a subscription fee to access and use the software, rather than purchasing and installing it on their own computers or servers. SaaS can be used for a variety of applications, such as customer relationship management (CRM), enterprise resource planning (ERP), and human resources management (HRM).
Standard Operating Procedure (SOP)
Standard Operating Procedures (SOPs) are step-by-step instructions that outline the procedures or processes required to complete a particular task or activity. They are often used in manufacturing, healthcare, and other industries to ensure that processes are completed consistently and safely. SOPs provide detailed guidance on how to carry out specific activities, including any necessary precautions, and can help to minimize errors, reduce variability, and increase efficiency.
Takt Time
Takt time is a term used in lean manufacturing and refers to the available production time divided by the customer demand for a product or service. It is essentially the rate at which products need to be produced to satisfy customer demand while also optimizing production efficiency. By calculating the takt time, manufacturers can adjust production to meet customer needs in a timely and efficient manner.
Tribal Knowledge
Tribal knowledge refers to information and knowledge that is not documented or shared in a formal way within an organization, but is instead passed down informally through conversation, observation, and experience. It is often based on the collective knowledge and experience of a group of individuals who have been with the organization for an extended period of time, and may include tips, tricks, and best practices for getting things done. However, because tribal knowledge is not documented or shared in a formal way, it can be difficult to transfer to new employees or to scale up operations.
Waste
Waste refers to the amount of material, energy, or resources that are discarded or lost during the production process. This waste can take many forms, including defective products, excess raw materials, scrap, rework, and wasted time. Reducing production waste is an important goal for many manufacturers, as it can lead to cost savings, improved efficiency, and reduced environmental impact.
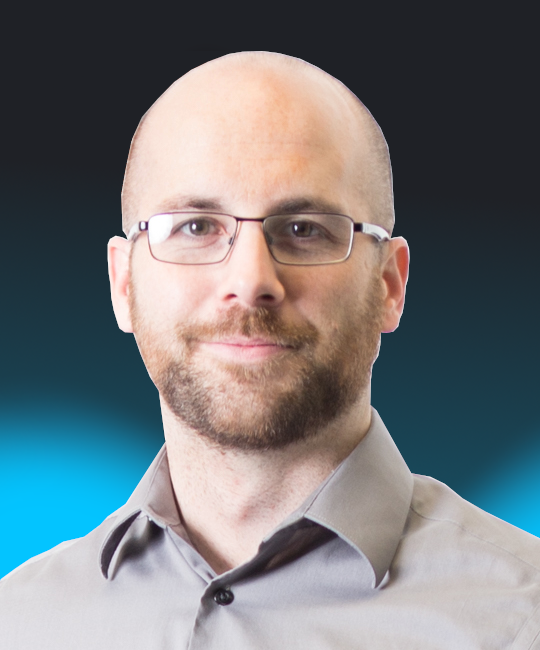
Ben Marsh
I've spent my career in Manufacturing, and can't stop trying to make things more efficient. At home, I am a master Lego builder with my son.