Every single shift of every single day will experience Operator Inactivity; it is a common phenomenon that significantly impacts your productivity. Generally, it falls into two distinct categories - Operator-induced Inactivity, derived from individual operator issues, and Operation-induced Inactivity, stemming from organizational shortcomings.
Operator-induced Inactivity arises when an operator's personal issues, lack of motivation, or distinct focus-lapse periods cause delays. Such instances can hinder your workflow and productivity significantly. Direct engagement of Leads and Supervisors is often the most effective strategy to overcome these issues. They can motivate and monitor operators closely, facilitating an environment that encourages productivity and consistent workflow.
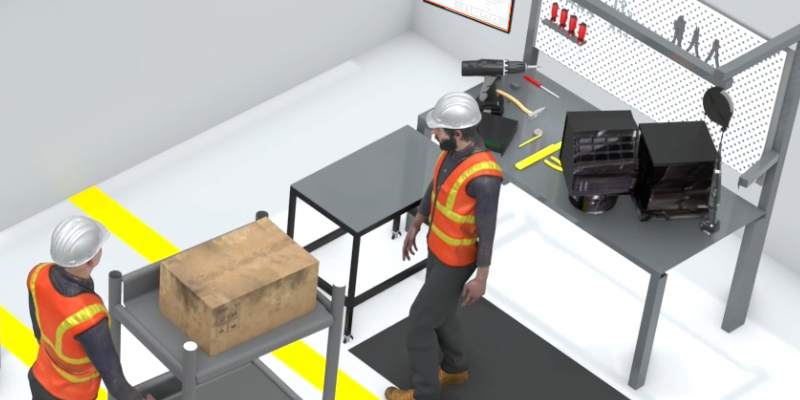
Contrarily, Operation-induced Inactivity is tied to your institutional challenges such as weak training programs, a lack of necessary resources, or existing procedural inefficiencies. If your factory has not yet transitioned to digital, addressing these issues requires a thorough examination and scrutiny of production lines and processes. Once you identify the root cause(s), appropriate solutions can be implemented to minimize disruptions and ensure smooth operations.
In my experience, this process can be simplified by adopting the perspective of a brand new employee. Asking questions such as, "What am I supposed to build, and how do I do it?" helps discern underlying issues, paving the way towards developing effective strategies that promote efficiency and productivity.
The Scout Systems Advantage
A significant portion of Operation-induced Inactivity can be mitigated utilizing digital work instructions, a prime advantage offered by digitized factories. Your Operators can be equipped with detailed, interactive access to daily production schedules, coupled with visual representations that guide them through the required steps to construct your product correctly. Embedded videos provide a seamless solution to understand complex tasks, drastically reducing the need for offline training. These visual aids streamline learning, ensuring a more efficient, uninterrupted manufacturing process. It's a smart blend of technology and practicality, saving time and enhancing productivity.
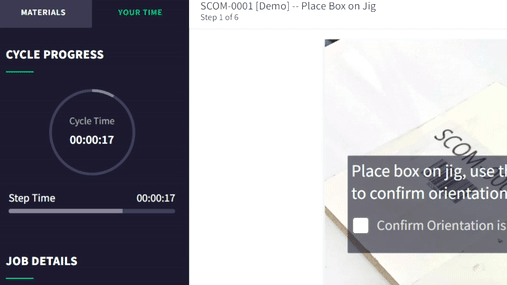
Another standout feature of the digital factory is having the capability to closely track the pace of production. Imagine your improved production rhythm if your Operators received prompt notifications if their progress rates fall below the anticipated speed. In the event the process is still failing your Operators, they can request assistance simply by pressing a button. This seamless facilitation of immediate help significantly reduces downtime and enhances overall productivity.
Catch Up with Innovation in just 3 Months
The advantages of a digital factory are truly transformative, revolutionizing operational efficiency and aiding in overcoming most Operation-induced Inactivity issues. If you feel that you are ready to transition to a digital factory, know that it can be done quickly and with minimal efforts of your staff. Scout System’s Accelerator Program is a 90-day blitz launching the platform with a focus on solving your pressing problems. You will have a dedicated Customer Success Representative that will become a part of your team and provide expert guidance. Reach out for a free consultation to see how this technology can assist in your growth.
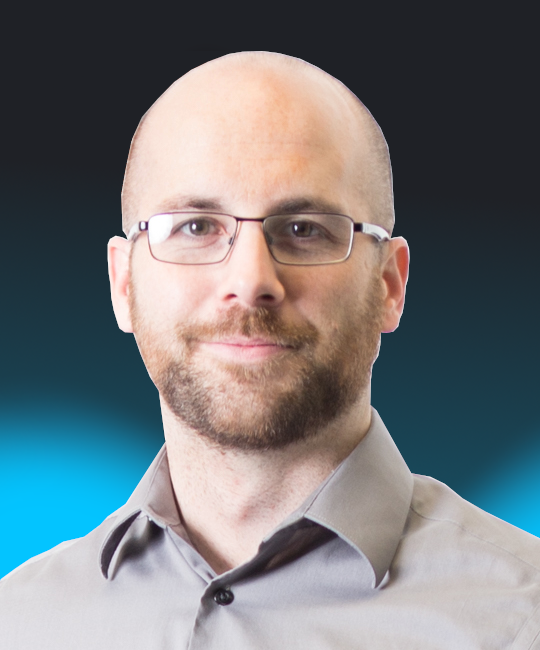
Ben Marsh
I've spent my career in Manufacturing, and can't stop trying to make things more efficient. At home, I am a master Lego builder with my son.