Rush jobs often compel production cells to abruptly shift gears, causing substantial waste. The time spent on setting up for a new job and the increased risk of damage to work-in-progress (WIP) due to potential mishandling can strain your resources considerably. Additionally, the hurried pace heightens the likelihood of your Operators overlooking crucial steps, compromising quality. Addressing rush jobs goes beyond time management - it's about preserving process integrity and quality, while minimizing waste and maintaining productivity.
The Balancing Act of Rush Jobs
In an analog factory Production Supervisors have limited real-time information. This typically results in Rush Jobs taking precedence over active orders. Instead, imagine if your Production Supervisors could be accurately informed when the Rush Job would finish if they allowed the active orders to complete without disruption.
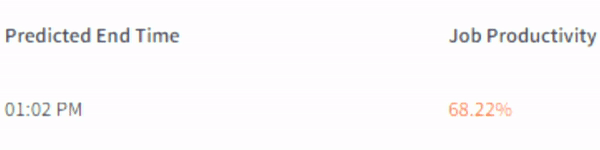
Manufacturers employing a Shop Floor Management system gain a notable edge in this situation. Advanced digital platforms, like Scout Systems, equip your staff with real-time data, offering predictive analysis on production order completion times. Leveraging such information can often reveal that pausing an ongoing job to accommodate a rush order may not be required. Therefore, digital integration into your manufacturing process not just optimizes efficiency but also arms your staff with insights for making informed, cost-effective decisions.
Halting and Resuming Production Orders
For jobs that must be halted due to reprioritization, your Operators will need to know if the last unit was completed or if it’s still a work in progress. If it wasn’t completed, what was the last task done? How many units remain for the order? Navigating the transition from completing a rush job back to the original production order can pose challenges, especially during a shift change.
Failing to clearly answer these questions will result in longer change over time and increased chances of defects. Digital work instructions fix this issue entirely. Your Operators simply press Suspend Job and move onto the rushed order. When they return to the suspended job, the platform returns them to the exact location the job was disrupted.
Improve On-Time Delivery in 90 Days
Transitioning to a digital factory has immense benefits, beyond assisting your factory when rushed. Scout System’s Accelerator Program is a custom tailored project where we work directly with you to implement our digital shop floor management platform. A dedicated Customer Success Representative will be assigned to your team and will help configure the technology to target your pressing challenges. In just 3 months customers discover increases in their capacity, reductions in their training time, and massive improvements to overall product quality. The majority of new customers achieve a return on their investment in a matter of months!
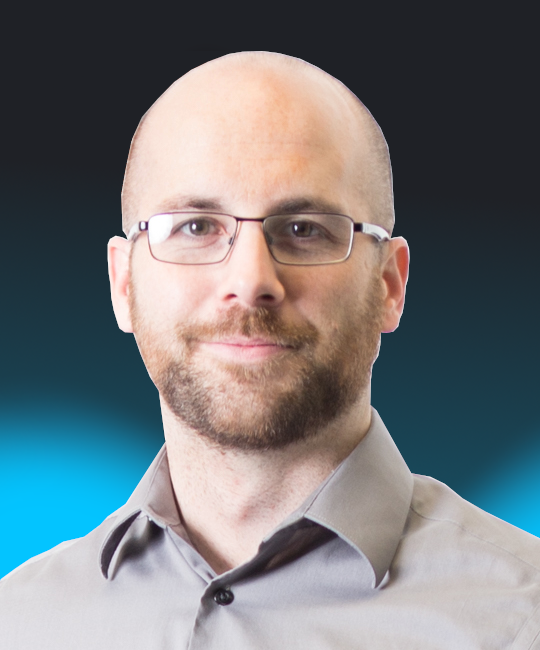
Ben Marsh
I've spent my career in Manufacturing, and can't stop trying to make things more efficient. At home, I am a master Lego builder with my son.