Precision in manufacturing is paramount. Each component must fit and function perfectly within its intended system.
Errors in assembly can lead to costly recalls, damaging both financials and reputations. Thus, adhering to clear, concise manufacturing work instructions is critical to maintaining quality and reliability in the final product.
Given the ever-evolving complexities of modern manufacturing, the importance of detailed and unambiguous work instructions for production cannot be overstated. These documents serve as the bedrock for assemblers, ensuring each step of the production process is executed with precision, efficiency, and adherence to specifications.
Clarity breeds excellence in production.
Crafting Clear Work Instructions
Clarity in manufacturing work instructions is paramount to prevent ambiguity and ensure consistent execution. This mandates precise language and sequencing in work instructions that leaves no room for interpretation or error.
Critical elements include diagrams, standardized terms, and step-by-step procedures, all pivotal in crafting manufacturing work instructions that are easily understood by your workers. These should be reviewed regularly to eliminate any potential for misunderstanding due to changes in processes or production methods.
Work instructions must be accessible, frequently referenced, and kept current to embody the manufacturing process's evolving nature and safeguard product quality.
Identifying Key Processes
Precision in assembly relies on delineating critical stages—each process segment must be meticulously identified and codified within manufacturing work instructions.
Effective assembly hinges on streamlining complexity into manageable and repeatable steps, catalyzing both accuracy and productivity.
To strategically pinpoint these vital processes, it is essential to dissect complex assemblies into granular tasks, sequentially organized and simplified to enable mastery by assemblers.
Recognizing and documenting key processes stabilizes production—anchoring a reliable foundation for manufacturing consistency and enabling a streamlined pathway to adept craftsmanship.
Choosing Simple Language
Select words that are clear and unambiguous.
The complexity of technical jargon can impede understanding. When crafting work instructions, opt for terminology that is straightforward—eschewing overly technical lingo that could confuse non-expert staff. Clarity should always outrank complexity to facilitate the highest level of comprehension among manufacturing personnel.
It's essential to prioritize concise phrasing—this aids in reducing potential ambiguity. Choose direct, plain words that convey procedures with precision, ensuring all assemblers can follow instructions without misinterpretation or confusion.
Avoid industry jargon unless absolutely necessary.
When the language is too complex or laden with industry-specific terms, it can intimidate or exclude team members who are not yet familiar with the lingo. It's recommended to provide a glossary if advanced terminology is unavoidable, fostering inclusivity and comprehension for all employees. Consequently, utilizing clear and concise language in work instructions is crucial for ensuring accurate translation, particularly in digital work instructions where auto-translation features are employed, thereby enhancing overall precision and minimizing the risk of errors or misinterpretation.
Standardizing Production Steps
Efficiency in assembly and fabrication hinges on the uniformity of procedures across the production floor. Such standardization mitigates variability and enhances repeatability, leading to consistent quality outcomes. By codifying each task, assemblers are equipped with a clear roadmap that delineates every required action, minimizing deviation and its attendant risks.
To bolster the efficacy of this uniform approach, assemblers must be trained to adhere to a "production script”. This script serves as the foundation of a shared language within the manufacturing landscape, strengthening the alignment among team members. In this context, success not only involves the accurate execution of steps but also rests on the team’s collective adherence to these standardized protocols which promote excellence and reliability in the final product.
Sequence and Flow
Proper sequencing in production is critical to prevent bottlenecks, ensuring each phase meshes seamlessly into the next. This ordered progression of operations contributes significantly to overall efficiency, as well as output quality.
Choreographing task transitions can minimize downtime and materials waste. It helps maintain a rhythm of production.
An optimized sequence is akin to a well-directed symphony—each section performs at the precise moment fostering a harmonious culmination with minimal discordance. When assemblers operate in sync, the throughput time is effectively reduced, and the potential for errors diminishes.
Flawless execution of the production sequence demands a meticulous approach to planning. This framework provides assemblers with a procedural compass, guiding them through complex tasks. It ensures that assembly stages are not only followed in sequence but are also executed employing best practices and innovation. In doing so, assemblers play a pivotal role in elevating the operational cadence to a new apex of excellence. Furthermore, a well-established "rhythm" can translate to a substantive improvement in customer satisfaction, owing to consistent and reliable output.
Tools and Materials Specifications
To guarantee precision outcomes, strict adherence to tools and material specifications is paramount. Assemblers must validate that every item aligns with the outlined standards before commencing tasks.
In detail, tools and equipment must conform to a meticulous calibration protocol. This encompasses regular maintenance, correct settings, and immediate rectification of discrepancies. Material specifications, pertaining to quality, dimensions, and tolerance levels, must equally be met with unwavering accuracy. Adherence to these parameters ensures the integrity of the final product, precluding the possibility of defects and ensuring customer satisfaction.
If a product goes through an Engineering change, the tools and materials may change as well. Critical to this process is the employment of a robust verification system. This involves scrupulous inspections and documentation review.
Safety and Quality Checks
Ensuring the safety and quality of products is paramount to maintaining confidence in the production process and end-product integrity.
- Conduct preliminary safety inspections before commencing operations, verifying that equipment and tools are in optimal working condition.
- Review material certifications to ensure that all inputs meet industry standards and project specifications.
- Employ calibrated measurement tools for exacting verification of dimensions and tolerances.
- Execute performance tests on prototypes to confirm operational functionality and safety.
- Document findings and initiate corrective actions if discrepancies or defects are identified.
Adherence to these checks is non-negotiable and requisite for advancing production stages.
A systematic approach to safety and quality not only mitigates risks but also streamlines production continuity and efficiency.
Rollout Strategies
Effective rollout strategies hinge upon meticulous planning and phased deployment. It's a delicate balance between swift implementation and thorough assimilation by the team.
Before introducing new instructions, it's best to pilot them in a controlled environment. This minimizes disruption and allows for real-time refinements before a full-scale launch.
Incremental rollouts enable teams to adapt progressively. As feedback is gathered and processed, subsequent phases can address emerging challenges and optimize processes accordingly.
Attention to detail when introducing new protocols is imperative. Each phase must be carefully monitored for compliance and effectiveness, ensuring that the transition is seamless and beneficial.
Ultimately, a well-executed rollout solidifies new instructions within the fabric of daily operations, promoting a culture of continuous improvement and operational excellence.
Evaluating Instructional Effectiveness
Work instructions must be reviewed both with data and Operator feedback. Factors such as speed of task execution, error rate reduction, and adherence to safety protocols are instrumental in determining whether the instructional materials are meeting their intended objectives. This evaluation also highlights the sustainability of practices instituted, ensuring they contribute positively to the operational cadence.
Frequently reassessing instructional content against the backdrop of evolving production technologies is paramount. Utilizing feedback loops from floor staff and management, alongside incident and performance reports, creates a dynamic instructional ecosystem that evolves in lock-step with the pace of innovation, maintaining an edge in a sector driven by continuous improvement and exactitude.
Feedback Mechanisms
Feedback Mechanisms are vital for refining work instructions and enhancing production efficiency.
- Real-time observation of operations to gauge instruction adherence
- Post-task debriefings with assembly teams to discuss challenges and improvements
- Quality control data analysis to identify recurring issues or successes
- Customer feedback collection for insights into final product satisfaction
- Incident report reviews to understand the precursors and outcomes of deviations
- Suggestion boxes or digital forums for anonymous or direct employee input
An agile response to feedback permits ongoing improvement and adaptation of work processes.
Incorporating a variety of feedback mechanisms ensures diverse input is captured, fostering a culture of continuous improvement.
Implementing Manufacturing Work Instructions
Microsoft Word/Excel and other legacy software systems are not recommended for making manufacturing work instructions. Even if your factory is not ready to make the switch to digital, Scout Systems offers a free work instruction software with not catch. Sign up and get immediate access to work instruction software with built in training guides and examples. By utilizing a commercial platform designed to create manufacturing work instructions, you will be able to create higher quality instructions in less time.
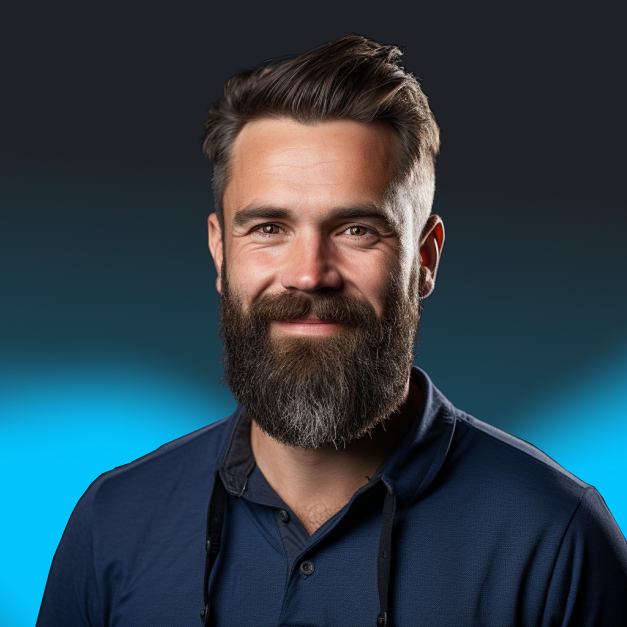
Richard Mason
By day I help people solve problems, by night I'm enjoying IPAs! For fun I work in my garage building gadgets that cost way more than they are worth.