The evolution of manufacturing work instructions has revolutionized how factories operate. From their origins in the Industrial Revolution to the refined systems of scientific management and mass production, these guidelines have been crucial to industrial success. They have evolved significantly, shaping the backbone of manufacturing efficiency and productivity.
Today, these work instructions provide detailed guidance for workers on executing specific tasks, ensuring precision and efficiency on the factory floor. This journey from paper to digital represents a significant shift in the manufacturing landscape. It marks a transition towards more streamlined, error-free operations.
At Scout Systems, we understand the critical role that manufacturing work instructions play in your business’s daily operations. Our latest insights delve into this evolution, highlighting the transformation from traditional manufacturing work instructions to modern digital solutions.
Here, we aim to equip you with the knowledge and tools necessary to navigate this shift, enhancing productivity and fostering growth in your manufacturing procedures.
Join us as we explore the past, present, and future of manufacturing work instructions in the industry. Discover how embracing digital transformation can propel your operations into a new era of efficiency and success.
The Evolution of Manufacturing Work Instructions
Manufacturing work instructions have journeyed from paper to digital, marking a significant evolution in the industry. This change reflects a broader shift from traditional to modern, streamlined operations.
In the past, paper-based manufacturing work instructions were the norm. Teams relied on printed manuals and documents. This approach, while straightforward, had its downsides. It was inflexible, prone to errors, and challenging to update.
The transition to digital work instructions represents a leap forward. Why? It's simple: clarity, consistency, and communication. Digital formats offer unprecedented precision. They allow for real-time updates and clearer guidance. This shift is not just about replacing paper instructions with screens; it's about enhancing the entire manufacturing process.
Smart Manufacturing Insights - The critical importance of Work Instructions
The move towards digital is driven by the need for efficiency and accuracy in production. In the fast-paced world of manufacturing, time is money, and mistakes are costly. Digital work instructions streamline operations, reduce errors, and improve productivity. They are accessible, easy to follow, and can be updated instantly to reflect process improvements or changes.
This evolution from paper to digital is not just a change in medium. It's a reflection of the industry's ongoing pursuit of excellence and innovation. As we delve into the motivations, challenges, and transformative power of this shift, we uncover the true impact of digital work instructions on the manufacturing landscape.
Motivations for the Transition to Work Instructions Software
The transition to work instructions in manufacturing was driven by the need to enhance efficiency, ensure product quality, and facilitate scalability in production processes. This shift not only optimized productivity but also significantly improved the training of new employees and process engineers. In return, it allowed for a smoother integration into the assembly line production process.
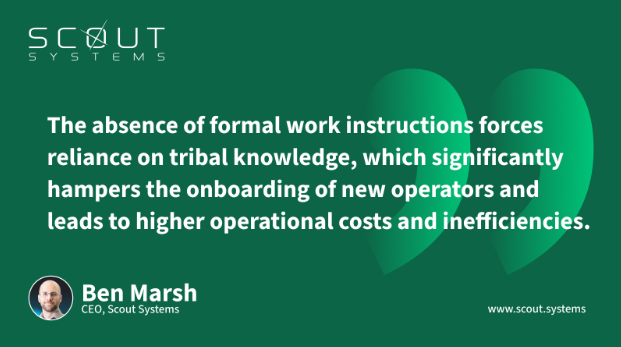
Recognizing the importance of standardized operational procedures, many organizations have developed work instruction templates to streamline this process. Traditionally, work instruction templates serve as a foundational tool. They enable companies to customize detailed instructions that cater to their particular tasks and operational needs.
These templates are often built on Microsoft Word, Excel, or PowerPoint (or the Google equivalent). If you're interested in seeing or downloading a manufacturing work instruction example, there are numerous online, or you can make a copy of this free template here.
Challenges of Outdated Work Instruction Methods
Traditional methods of manufacturing work instructions are often rooted in paper documentation or static digital files and face numerous challenges. These outdated practices can significantly hinder a manufacturing company or facility's efficiency and adaptability.
One major issue is the lack of real-time updates. Paper manuals or static files do not allow for instant revisions, leading to outdated or incorrect information being used on the factory floor. This can result in costly errors, decreased product quality, and increased waste.
Additionally, traditional methods often lack interactivity and visual clarity, making it harder for workers to understand complex processes. This can prolong training times and reduce overall efficiency, as employees may struggle to follow written instructions more accurately. Furthermore, paper-based instructions are prone to damage and loss, leading to further inefficiencies and potential safety risks.
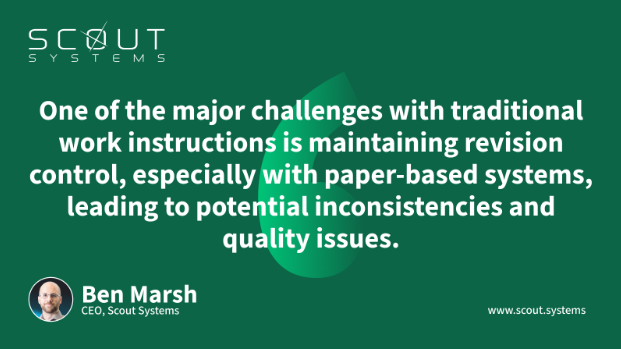
Another significant limitation is the difficulty in tracking compliance and understanding workflows. Without digital tracking, it's challenging to ensure that all workers follow the most current safety procedures or identify which steps may be causing bottlenecks or errors.
The lack of customization and scalability in traditional work instruction methods also presents a problem. As each manufacturing operation has unique needs, the one-size-fits-all approach of paper and standard manufacturing work instructions can be inadequate.
This results in a failure to produce quality products that meet specific operational requirements and hinders the ability to scale processes efficiently as a company grows.
The Emergence of Work Instruction Software in the Manufacturing Process
As manufacturing processes advanced, Work Instruction Software companies emerged, developing sophisticated solutions. These were developed to streamline the creation, distribution, and management of standard manufacturing work instructions. These companies have addressed the evolving needs of the industry, simplifying complex procedures and enhancing operational efficiency.
The advent of such software reflects a broader trend toward Industry 4.0, where connectivity, automation, and data analytics converge to optimize production workflows.
The benefits of using Work Instruction Software are substantial and cannot be overlooked, especially when compared to traditional methods like Excel and Word. While these conventional tools have been instrumental in documenting processes, they fall short in today's dynamic manufacturing environments.
Work Instruction Software transcends these limitations by offering advanced features that are not available in Excel or Word, such as tool integration and data analytics. Scout Systems offers Work Instruction Software for free to help manufacturers embrace this technological shift with zero expense to their organization.
Undoubtedly, Work Instruction Software will become a key pillar of the Lean journey in the years to come.
How to Prepare Your Factory for the Future
Preparing your factory for the future requires strategic foresight and proactive measures, particularly in documenting and optimizing your most skill-intensive processes.
Begin by identifying tasks that demand high levels of expertise and precision and prioritize these for detailed documentation. Utilizing work instruction software is a highly effective approach, as it facilitates the creation of clear, comprehensive instructions for specific tasks.
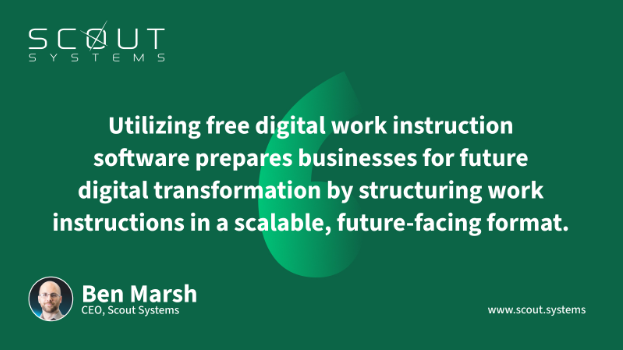
If resources are limited, starting with free work instruction software can also serve as a valuable initial step. This documentation process is crucial for several reasons. First, it ensures that critical knowledge and skills are captured and preserved, safeguarding your operations against the potential loss of skilled workers. Second, it lays a solid foundation for scaling your operations, as standardized work instructions streamline the training of new employees and ensure consistency in quality and productivity.
By taking the next steps, you're not just preparing for the future; you're actively shaping it. You are building a resilient and adaptable manufacturing environment that can thrive amidst the challenges and opportunities ahead.
Step-by-Step Instructions for Implementing Digital Work Instructions
Adopting digital manufacturing work instructions requires a strategic approach to ensure a smooth transition and effective integration into manufacturing processes. The first step involves assessing current workflows to identify areas where digital instructions can have the most impact. Focus on processes that are complex, prone to errors, or frequently updated. This initial assessment lays the groundwork for a targeted implementation strategy and effective manufacturing work instructions.
Once key areas are identified, the next step is selecting the right Work Instruction Software. Look for solutions that offer user-friendly interfaces, customization options, and compatibility with existing systems.
Training is a critical component of the strategy. Employees need to understand how to use the new software effectively. Develop comprehensive training programs that cater to different learning styles and levels of tech-savviness. Interactive sessions, hands-on workshops, and ongoing support can facilitate smoother adoption and reduce resistance to change.
Moreover, establish a feedback loop. Encourage employees to provide input on the digital work instructions' usability and effectiveness. This feedback is invaluable for continuous improvement and ensuring the instructions meet the workforce's needs.
Finally, integrate digital work instructions into the company's continuous improvement culture. Highlight good manufacturing work instructions and their role in enhancing efficiency, reducing errors, and supporting lean manufacturing initiatives.
By framing digital work instructions as a tool for empowerment and growth, companies can foster a positive attitude towards this technological shift.
Adapting to Digital: Overcoming Common Hurdles
Transitioning to digital work instructions software presents several hurdles. However, with strategic planning, these challenges can be overcome. The first major hurdle is resistance to change. Employees accustomed to traditional methods may be skeptical or apprehensive about new technology.
Address this by emphasizing the benefits of digital instructions, such as easier access to up-to-date information and reduced risk of errors. Engage employees early in the transition process, allowing them to voice concerns and become part of the solution.
Another challenge is the digital divide. Not all employees may have the same level of technical proficiency. To bridge this gap, provide tailored training sessions. Start with basic digital literacy for those who need it, followed by specific training on the new work instruction software. Ensure that support is readily available to help employees troubleshoot issues as they arise.
Data security and integrity also pose significant concerns. As work instructions go digital, protecting sensitive information becomes crucial. Select work instruction software with robust security features and establish clear protocols for data handling. Educate employees on best practices for data security to prevent breaches and ensure that proprietary information remains safe.
Finally, integrating new software into existing systems can be complex. Some companies might struggle with resources while implementing a new system. Work closely with IT specialists to ensure smooth integration and minimize disruptions to the production line. Test the software thoroughly before full-scale implementation and be prepared to address compatibility issues.
Smart Manufacturing Insights - Challenges in Work Instruction Software
By addressing these hurdles head-on, manufacturers can successfully navigate the transition to digital work instructions, paving the way for more efficient, agile, and resilient operations.
The Transformative Power of Digitalization in Manufacturing
The notion that digitalization represents an unprecedented advancement in manufacturing might seem hyperbolic. This is especially true when considering the monumental strides made during each Industrial Revolution. Yet, a closer examination of these transformative periods reveals the unique and profound impact of digitalization.
- First Industrial Revolution - Initiating in the late 18th century, this era was characterized by the shift from hand production methods to machines. The introduction of mechanization provided workers with superior tools, significantly enhancing productivity and setting the stage for future advancements.
- Second Industrial Revolution - Nearly a century later, the advent of new energy sources such as electricity, gas, and oil propelled productivity to new heights. This era harnessed the power of energy to fuel mass production, reshaping the manufacturing landscape.
- Third Industrial Revolution - Marked by the groundbreaking inventions of Programmable Logic Controllers (PLCs) and robots, this period introduced automation into manufacturing. The ability to produce higher-quality products with minimal human intervention was a game-changer.
Currently unfolding, this revolution is distinguished by its incompleteness and the vast potential it holds. Unlike its predecessors, Industry 4.0 extends beyond mere production enhancements, bridging productivity gains from the factory floor to the office. Rooted in digitalization, it leverages the virtual world to pioneer new forms of automation and connectivity.
The Fourth Industrial Revolution is not just another phase in manufacturing evolution; it is a paradigm shift that integrates the physical and digital worlds. The opportunities for productivity and innovation it presents are boundless, promising to redefine what is possible in manufacturing work instructions.
As we navigate through this era, the full scope of its impact remains to be seen, signaling an exciting chapter in the history of industrial advancement.
The Future of Manufacturing Work Instructions
The future of good manufacturing work instructions is clear: digital transformation is not just an option; it's a necessity. Embracing digital work instructions is essential for any manufacturing entity aiming to stay competitive and efficient.
In this digital era, the transition from paper-based to digital methods represents a fundamental shift towards a more agile, informed, and efficient manufacturing process.
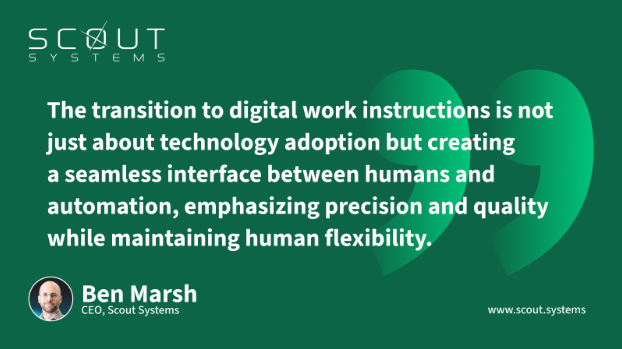
Scout Systems offers sophisticated manufacturing work instruction software designed to meet the modern demands of manufacturing environments. Our solutions are crafted to streamline the creation, distribution, and management of work instructions. Therefore, they enhance efficiency, reduce errors, and ensure consistent product quality.
As we move forward, the integration of digital work instructions will become increasingly central to manufacturing success. Scout Systems is here to guide and assist manufacturers in this journey, providing tools and expertise that pave the way for a smoother, more efficient, and future-proofed production process.
If you're looking to transform your manufacturing operations and embrace the future of work instructions, contact Scout Systems today. Let us help you harness the power of digitalization and set your factory on the path to success.
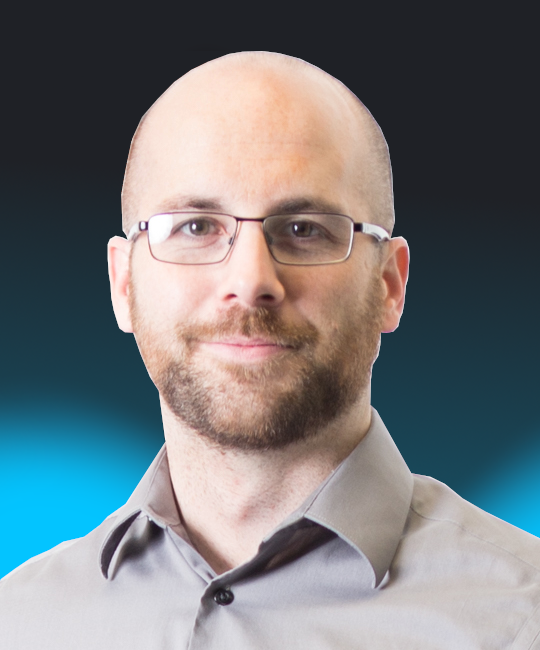
Ben Marsh
I've spent my career in Manufacturing, and can't stop trying to make things more efficient. At home, I am a master Lego builder with my son.