Envision yourself as an Operator, and picture a scenario where, one day, three senior managers position themselves a mere few steps away, intently observing every move you make. They remain silent, merely documenting your actions without any interaction. As weeks unfold, these very managers introduce a new data collection system to your production area. Technicians come in, set up the system, and guide you through the process before leaving you alone with this new technology.
This situation might stir a whirlwind of thoughts within you. Questions like "Is this system intended to replace me?" or "Have I been underperforming?" may haunt your thoughts. The introduction of data collection systems, especially when done abruptly and without proper communication, can significantly dampen an Operator's morale and even lead to resistance or sabotage of the project. However, securing the buy-in of your team can markedly enhance the project's outcomes and the overall success of your organization. Let's explore strategies to achieve this buy-in and ensure the successful integration of new technologies.
Start by Precisely Outlining the Project Objectives
Before implementing a data collection system, it's crucial to have a crystal-clear understanding of its necessity. Steer clear of vague justifications such as "we aim to boost our capacity." Instead, pinpoint the exact motivation behind the initiative, for example, "our principal client is demanding a 3% cost reduction this year, and to achieve this, we require precise data to gauge our progress."
Providing specific reasons can motivate your Operators to welcome the new technology and actively contribute to achieving the desired outcomes. While the notion of "increasing capacity" might seem like an additional burden to your Operators, framing it as a means to meet a key customer's expectations can be perceived as enhancing job security.
Understanding the objectives is also crucial for choosing the appropriate data collection method. In the contemporary landscape of Industrial Internet of Things (IIoT), a plethora of platforms are available. Selecting a platform that resonates with your organizational goals is a key factor in ensuring the success of this project.
Gather Operator Opinions and Perspectives
Your Operators possess a distinct viewpoint on your operations, often offering insights that might elude even your most experienced Manufacturing Engineers. Engaging your Operators early in the project can illuminate specific needs, leading to the selection of a data collection system that aligns well with everyone involved. By involving them in the decision-making process and informing them that their input influenced the choice of technology, you grant them a sense of ownership from the outset. This approach not only fosters a collaborative environment but also ensures that the system implemented is the most fitting for your operations.
Configuration Example: Digital Work Instructions
If the data collection platform that best suits your organization is Scout Systems' Work Instruction Software, a significant opportunity arises within the PAUSE screen of Compass. This feature allows each unique work area within the platform to be tailored to meet its specific challenges. It's crucial that the reasons for pausing reflect obstacles that hinder productive workânot operator errors, but broader organizational challenges.
During the initial setup phase, it's wise to involve your Operators in defining the specific pause reasons. This is an opportunity to listen to your Operators and let them identify the issues they find most obstructive. For instance, if they frequently find themselves waiting for material deliveries, including a "Waiting for Forklift" pause reason can be very relevant.
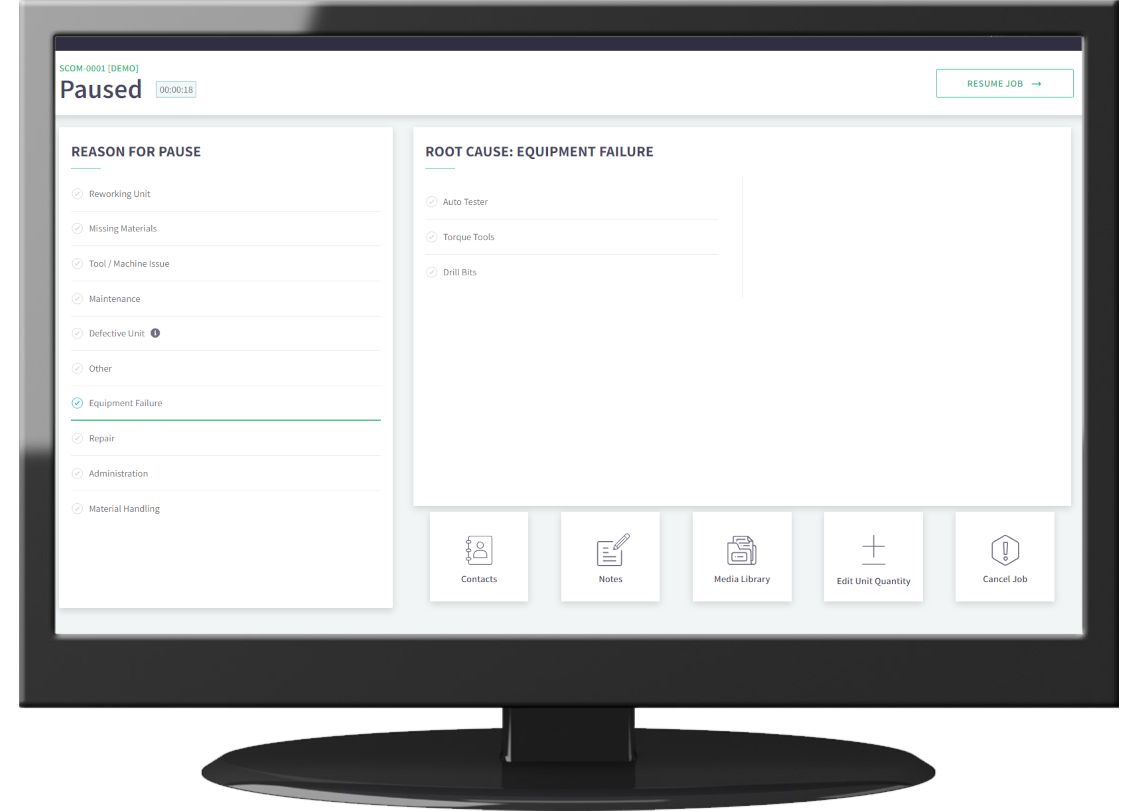
This collaborative approach in determining pause reasons not only ensures that the reasons are relevant and comprehensive but also encourages Operators to accurately report interruptions. Tailoring pause reasons to reflect general operational challenges, rather than personal activities like "using the bathroom," helps maintain the focus on enhancing overall company efficiency rather than appearing to micromanage individual Operators.
It has been observed that Operators skeptical of a data collection system tend to default their pause reason to 'Other'. This issue can be effectively addressed by educating Operators that 'Other' should exclusively represent personal matters. Activities such as bathroom breaks, HR visits, or making personal calls are all encapsulated under 'Other'. All other selections should reflect on the ways in which the company's processes might be falling short.
By clarifying this distinction, Operators begin to grasp the intended use of the 'Other' category, leading to a significant decrease in its selection. This understanding not only enhances the accuracy of the data collected but also shifts the focus towards identifying and addressing organizational inefficiencies. As Operators become more comfortable with this concept, the quality of the data improves, offering clearer insights into operational challenges and areas for improvement.
Utilize the Collected Data
It might seem self-evident, yet it's surprisingly common for companies to halt their progress at the data collection phase. Collecting data without any intention or plan to analyze and act upon it renders the entire exercise futile. This issue isn't exclusive to advanced shop floor management systems; it's a problem that can arise in even the most basic operational setups.
For instance, in factories where Operators are required to complete paperwork for every production order, it's not uncommon to hear frustrations about the accumulating stacks of unutilized documents. Operators often feel that their efforts in filling out these forms are in vain if they observe no actionable outcomes derived from their input. This sentiment reflects a broader issue: the perception of wasted effort on tasks perceived as non-value-adding from the workforce's perspective.
The key takeaway here is the critical importance of not just collecting data but actively using it to inform decision-making processes, improve operations, and address inefficiencies. Without the application of collected data, the effort invested in its gathering is indeed, as the Operators suggest, a waste of time. For a data collection initiative to be truly valuable, it must be part of a larger strategy that includes analysis, insight generation, and actionable outcomes that lead to continuous improvement.
Simple Steps to Make Improvements with Data
Starting with the Non-Value Added (NVA) report is an excellent strategy for leveraging production data to drive improvements. This production report generates a Pareto chart, which can be segmented by Operator, Product, or Station, offering a clear visual representation of where inefficiencies are most pronounced. The power of the Pareto chart lies in its ability to highlight the principle of 'the vital few': that a small number of causes are often responsible for a large portion of the problem.
By clicking on each of the vertical bars in the chart, users can drill down into the specific Root-Cause issues underlying the non-value added activities. This functionality not only simplifies the identification of operational bottlenecks but also facilitates a targeted approach to problem-solving.
Utilizing the NVA report in this way can illuminate the most significant challenges facing your operations. It provides a straightforward and effective tool for pinpointing where efforts to eliminate waste and enhance efficiency should be concentrated. By systematically addressing the issues identified through this analysis, organizations can make substantial strides in improving their overall productivity and operational effectiveness.
Once the primary challenges have been pinpointed using the Non-Value Added report, the Production History report can provide further insights into the nature of these problems. This report offers a detailed view of how and when issues occur within your production processes. It can reveal whether your operation faces a few major issues that sporadically disrupt production or if there are constant, albeit brief, interruptions that cumulatively impact efficiency.
Understanding the frequency and duration of these problems is crucial for formulating effective solutions. If the issues are infrequent but significant, strategies might include implementing robust preventive measures or developing contingency plans to mitigate their impact when they do occur. On the other hand, if the problems are frequent but short-lived, this might indicate systemic inefficiencies that require process optimization or continuous improvement initiatives.
Armed with this knowledge, Manufacturing Engineers can tailor their approach to problem-solving, ensuring that their efforts are directed towards the most effective interventions. This nuanced understanding of production challenges enables a more strategic allocation of resources, whether it be in training, equipment, process redesign, or other corrective actions, ultimately leading to a more efficient and productive operation.
Share the Wins
As you start addressing the issues on your production floor, the benefits derived from these improvements will accrue and perpetuate over time. For instance, achieving and sustaining a 25% reduction in waste translates into ongoing operational efficiencies month after month. An effective way to capitalize on these gains and foster a culture of continuous improvement is by sharing the successes with your Operators.
Rewarding your team with tangible benefits such as gift cards, bonuses, or additional time off not only serves as a token of appreciation for their contributions but also significantly boosts motivation. This approach reinforces the value of their efforts towards achieving operational excellence and encourages them to actively participate in and support continuous improvement initiatives.
When executed thoughtfully, such rewards can galvanize your Operators, fostering a sense of excitement and commitment towards embracing continuous improvement practices. Moreover, it builds trust and confidence in management's approach to implementing change, creating a more cohesive and proactive workforce. This positive reinforcement cycle not only enhances productivity but also contributes to a more engaged and satisfied team, driving further innovations and efficiencies in your operations.
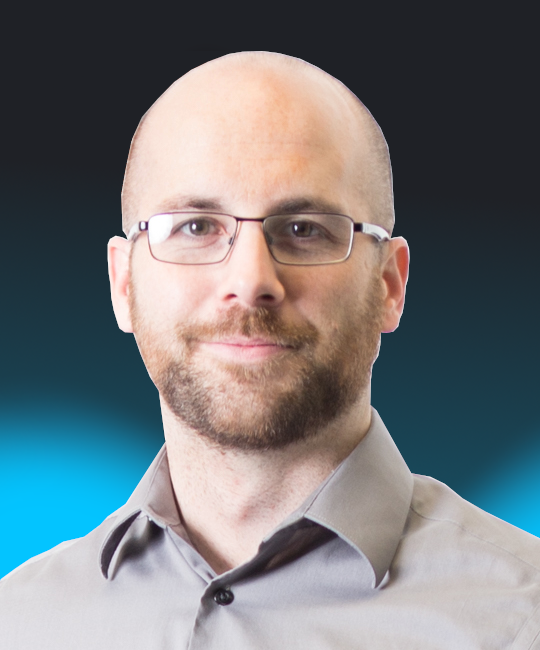
Ben Marsh
I've spent my career in Manufacturing, and can't stop trying to make things more efficient. At home, I am a master Lego builder with my son.