Is your fabrication team currently grappling with outdated paper-based work instructions, resulting in inefficiencies and errors?
Embracing digital work instructions can revolutionize your operational workflow, ensuring precision and real-time updates - attributes essential for impressing discerning clients.
So what exactly is the difference between the two? Let's dive in!
Traditional Work Instructions Defined
Traditional work instructions are an indispensable tool, serving as the blueprint for assembly and fabrication operations. They guide technicians through the intricacies of complex tasks, ensuring consistency and quality in the outcomes of production processes.
Predominately, these instructions come in paper format or static digital documents such as PDFs. They contain step-by-step procedures, visual aids, and important safety information that must be adhered to meticulously in order to achieve the desired precision in product assembly and quality.
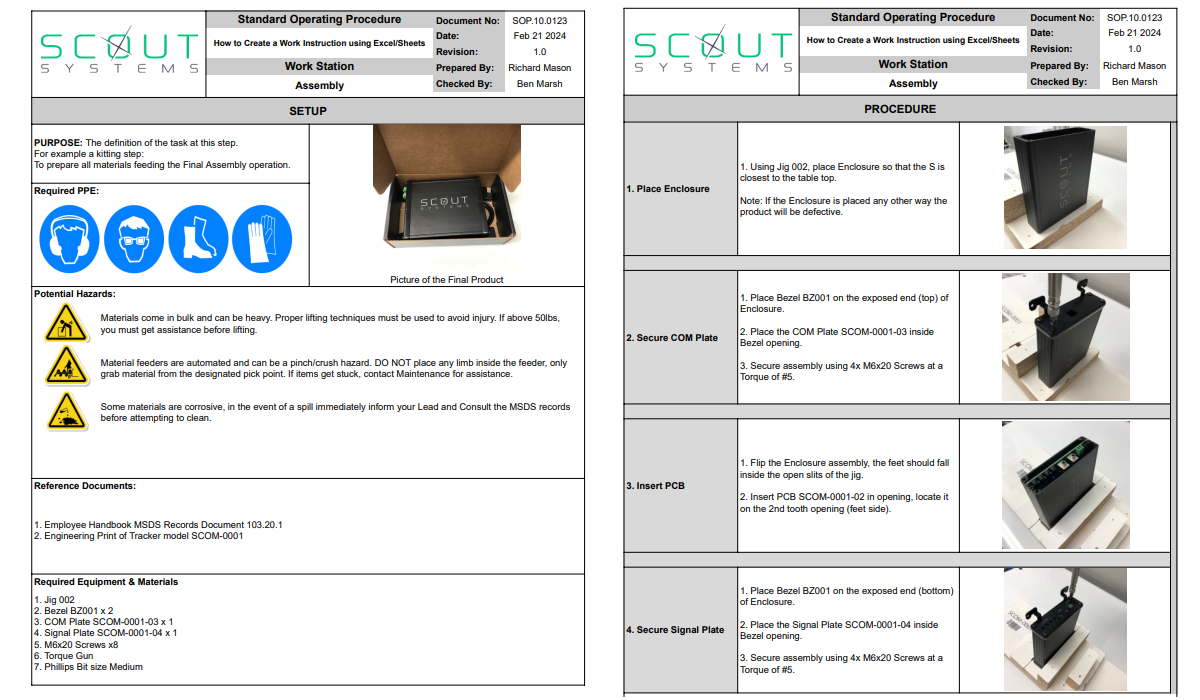
The term "hardcopy" and "paper-based" are often synonymous with traditional work instructions, underscoring their tangible, physically unmodifiable nature once they are distributed to the shop floor.
Characteristics of Conventional Methods
Conventional work instructions rely on paper documents, which can be cumbersome and difficult to update. It's a static form of communication, resistant to real-time adjustments and immediate feedback loops.
In an era dominated by digital transformation, conventional methods might seem archaic. They are detached from dynamic data platforms, hindering their integration with modern production technologies and systems.
Conventional instructions cannot match the pace of today's ever-changing manufacturing landscapes.
With traditional methods, information dissemination is slow and updates are labor-intensive. This introduces a greater potential for outdated practices to persist, and when modifications occur (often through supplementary notes or reprints), comprehensiveness and prompt distribution can be a significant challenge.
Implementation in the Workplace
Traditional work instructions, when introduced into the workplace, are an exercise in control and stability. They form the backbone of established manufacturing protocols, reflecting an organization's commitment to consistent and tried-and-true practices.
However, their transition to digital work instructions marks a paradigm shift towards agile and adaptive operations. By embracing digital solutions, organizations facilitate real-time communication and updates, empowering workers with the most current information. This digital conversion allows for an enhanced collaborative environment, where insights from various stakeholders can be integrated quickly into the workflow. The result is a more responsive and intelligent system that can react and adapt to changing conditions or requirements.
Importantly, the deployment of digital instructions is not without its challenges. The transition requires a thoughtful restructuring of existing procedures, a commitment to training personnel, and an investment in necessary hardware and software infrastructure. Yet the long-term benefits typically outweigh these initial efforts, as digital instructions often lead to improved efficiency, error reduction, and a higher level of detail and accuracy in the execution of tasks.
The adoption of digital instructions also sets a foundation for more advanced manufacturing innovations. Indeed, it enables the integration of cutting-edge technologies, interactive guidance or real-time analytics for continuous process improvement. It represents a decisive move towards a future-oriented workplace, where technology elevates the role and productivity of human workers, aligning with both market and customer expectations for quality, efficiency, and innovation.
Digital Work Instructions Unveiled
Transitioning to digital work instructions represents a fundamental shift in the realm of assembly and fabrication, enabling immediate access to rich, dynamic content including images, videos, and real-time feedback loops. This medium fosters enhanced communication, precision, and compliance with the most up-to-date production standards, ensuring that operations are performed seamlessly and effectively.
By embracing the digital format, companies can rapidly update and disseminate vital procedure changes across the relevant departments, mitigating the risk of outdated practices and ensuring consistency in the quality of the end products delivered to discerning clientele.
Key Features and Technologies
Digital work instructions often incorporate interactive elements and multimedia, to guide and engage operators more effectively. They also frequently leverage real-time data analytics to optimize task execution and process efficiency.
Furthermore, innovative technological integrations, like Internet of Things (IoT) devices, collect and synchronize operational data instantaneously.
Integrating these systems often includes robust cybersecurity measures to protect critical manufacturing data, a vital component considering the sensitive information involved.
Lastly, cloud-based storage and access solutions are typical to ensure that digital instructions are always up-to-date and readily available to authorized personnel.
Benefits of Going Digital
Transitioning to digital work instructions provides an immediate boost in efficiency and accuracy.
- Real-time Updates: Instant dissemination of changes and new protocols.
- Enhanced Accessibility: Critical instructions are available anytime, anywhere.
- Multimedia Integration: Use of visuals and videos for clearer understanding.
- Data Analytics: Continuous improvement through tracked performance metrics.
- Reduced Paperwork: Significant decrease in paper consumption and clerical errors.
- Customizable Content: Personalized instructions for different roles or expertise levels.
With digital instructions, important information is less prone to misinterpretation.
Adopting digital work instructions fortifies the precision and adaptability of manufacturing processes.
Comparing Usability and Efficiency
Digital work instructions significantly elevate the usability of procedural content, leveraging interactive elements, such as inputs, videos and animations. These features conduce to an intuitive user interface, enabling workers to rapidly assimilate and apply new directives, thus substantively minimizing training durations and promoting a swifter adoption curve. This improves not only the speed but also the quality of performance, as workers are guided through complex tasks with enhanced clarity and precision.
Conversely, traditional paper-based instructions struggle to match the immediacy and efficacy of their digital counterparts. Physical manuals lack dynamic interactivity and are often more time-consuming to navigate. This can lead to protracted information retrieval and increase the likelihood of errors in task execution. The digitization of work instructions represents a transformative leap in operational efficiency, offering a more seamless and error-resistant methodology for the dissemination of critical manufacturing knowledge.
Integrating with Emerging Tech Trends
As production systems become progressively interconnected, the role of digital work instructions is paramount in leveraging the potential of these sophisticated networks.
To stay current, digital work instructions must seamlessly interact with advanced technologies such as Artificial Intelligence (AI) and the Internet of Things (IoT). These integrations promise to revolutionize the landscape of manufacturing, offering unprecedented levels of automation and predictive maintenance, thereby aiding in the refinement of assembly processes.
The incorporation of digital work instructions into advanced manufacturing systems supports the transition towards smart factories. As automation and data-driven insights become more prevalent, it is essential to develop digital instructions that are not only responsive to real-time manufacturing feedback but also predictive in nature. These smarter systems foster a landscape where real-time adaptability and proactive troubleshooting become a reality, enhancing productivity and sustaining competitive advantage.
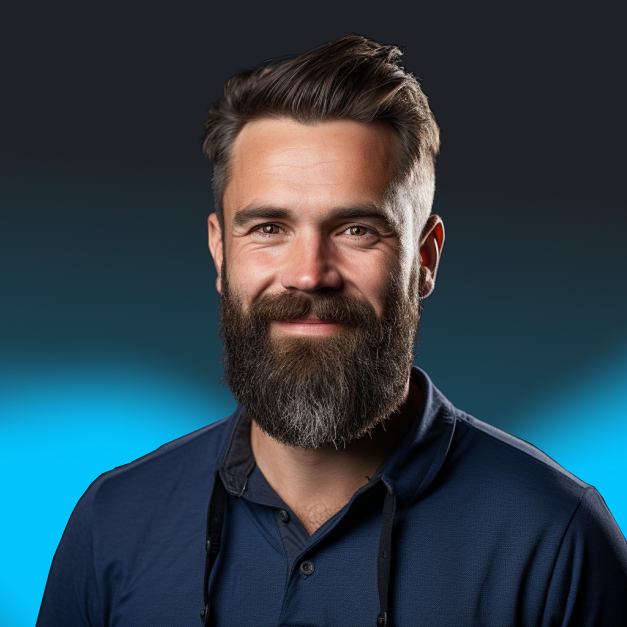
Richard Mason
By day I help people solve problems, by night I'm enjoying IPAs! For fun I work in my garage building gadgets that cost way more than they are worth.