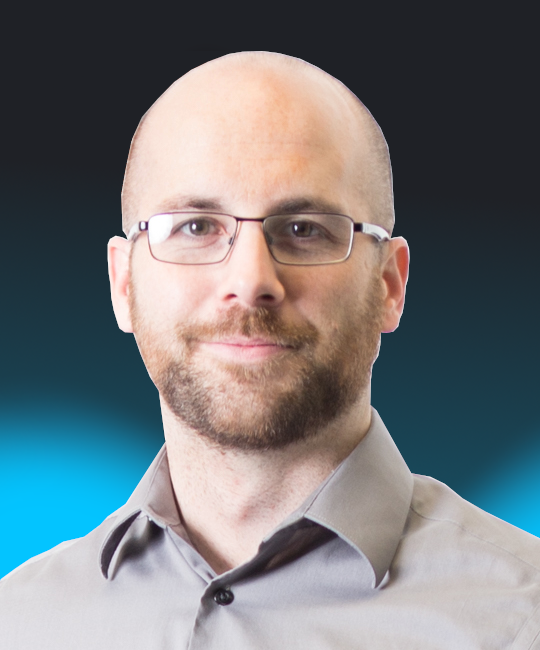
Ben Marsh
I've spent my career in Manufacturing, and can't stop trying to make things more efficient. At home, I am a master Lego builder with my son.
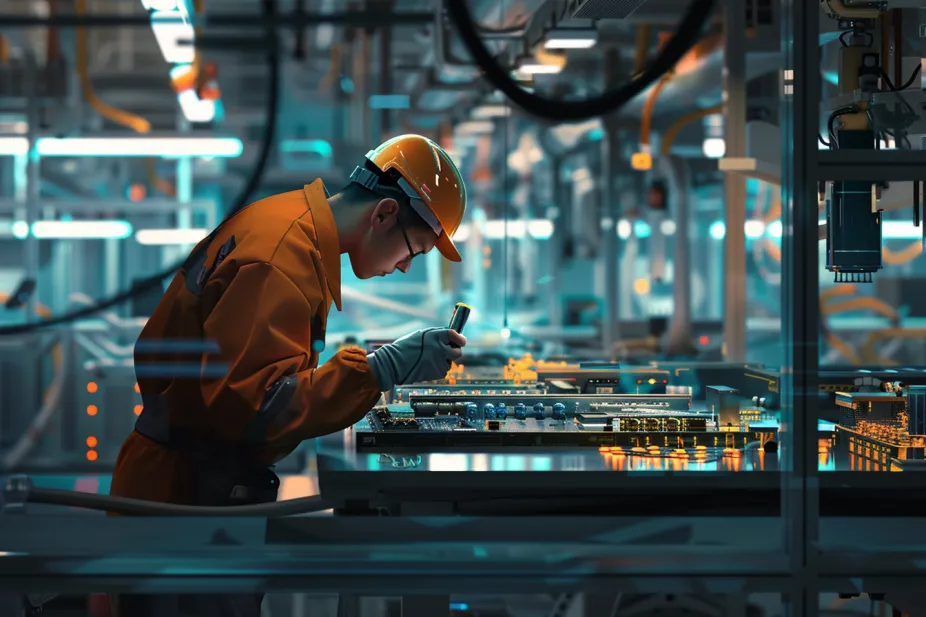
How Smart Tool Integration Transforms Manufacturing
Transform manufacturing with Smart Tool Integration for precise torque control and reduced errors. Scout Systems' Work Instruction Software ensures seamless tool management and automation.
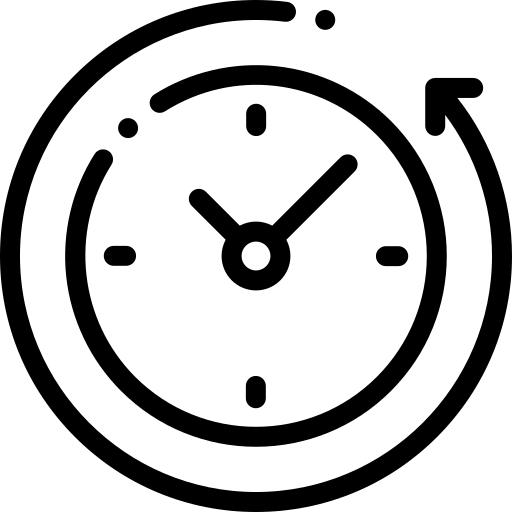

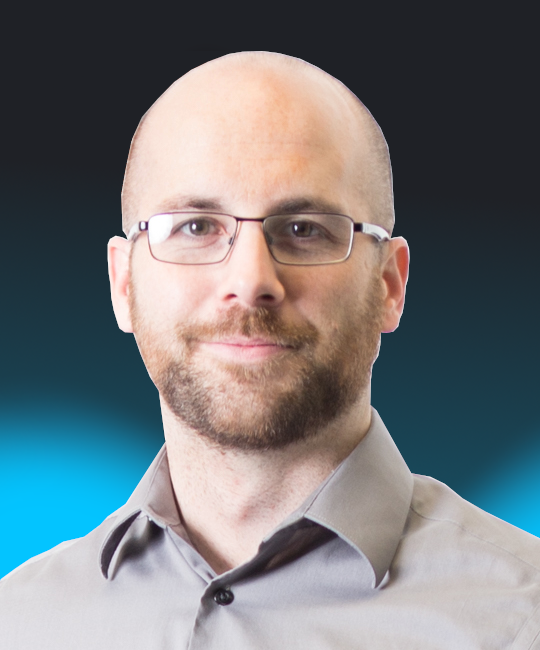
Ben Marsh

Critical Key Performance Indicators for Manufacturing
Monitoring these key performance indicators for manufacturing allows facilities to enhance productivity and optimize their processes.
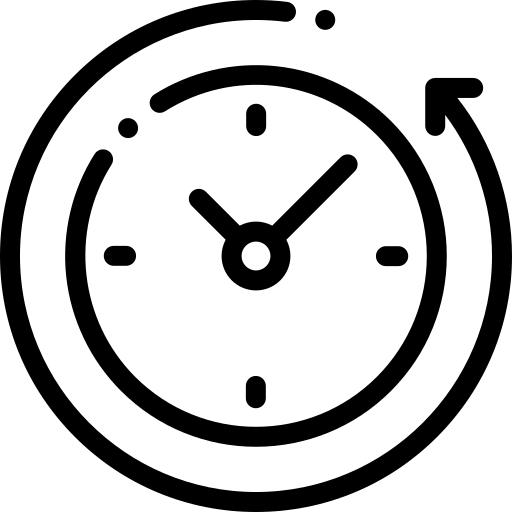

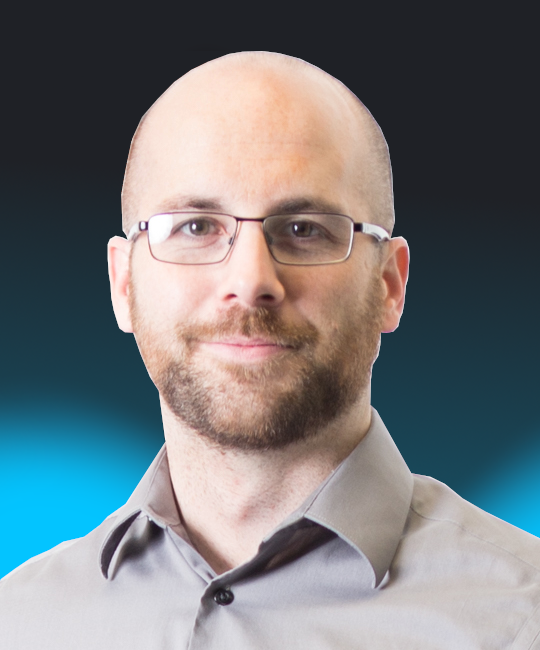
Ben Marsh

How to Utilize Data Collection Systems
Exploring actionable data sets and practical strategies for implementing cost-effective changes immediately. Simplifying data collection systems along the way.
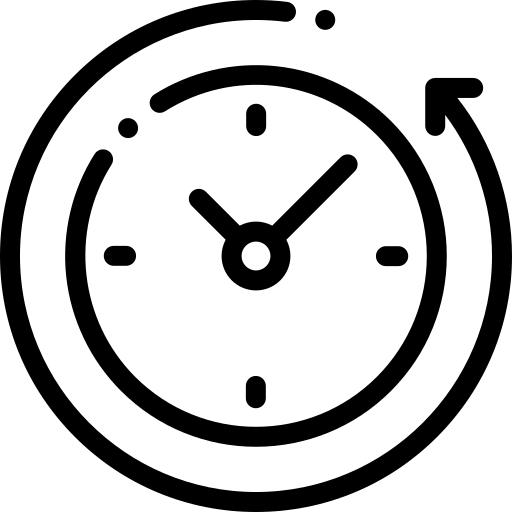

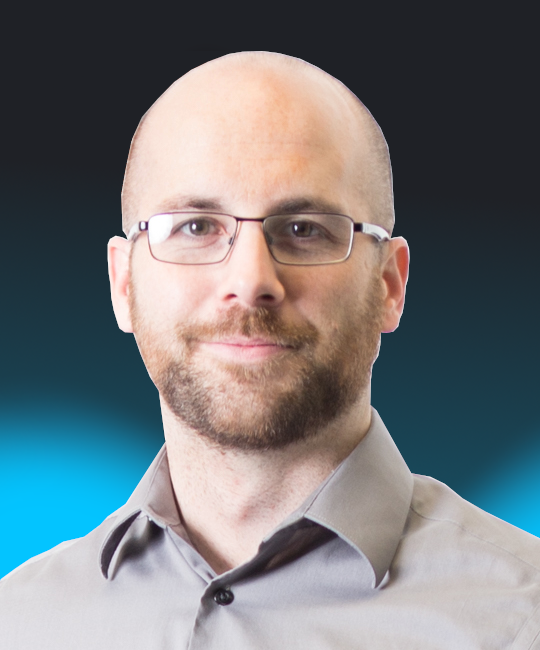
Ben Marsh
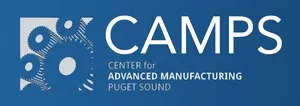
Learn How to Integrate Shop Floor Management Systems
A week from today (May 1st), I'll be presenting to Center for Advanced Manufacturing Puget Sound (CAMPS) on the topic of understanding data and how manufacturers can integrate it. You can register for the free event below. Let's touch briefly on what you can expect.
Register
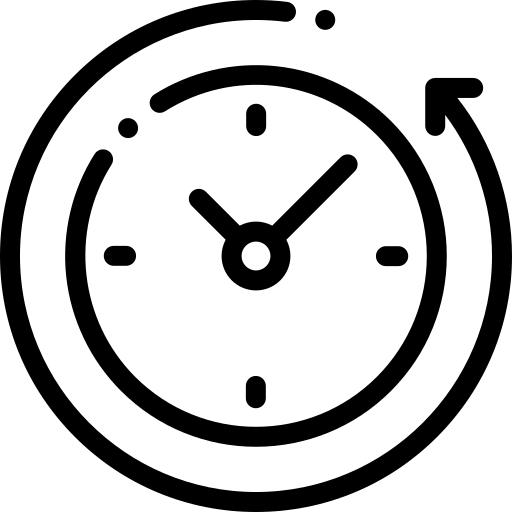
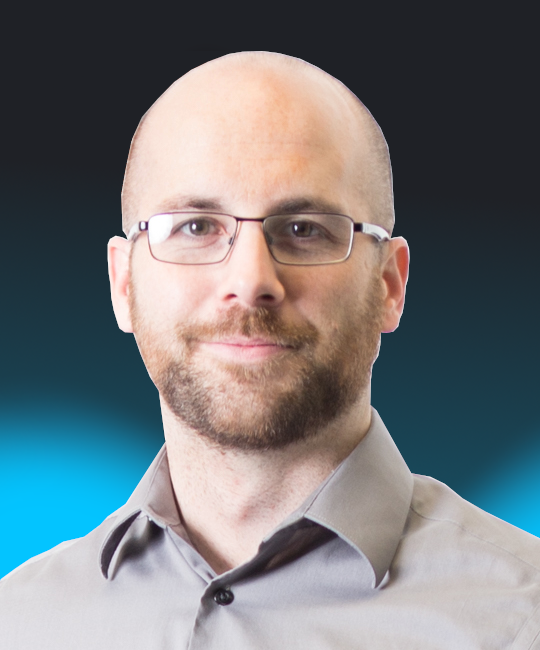
Ben Marsh
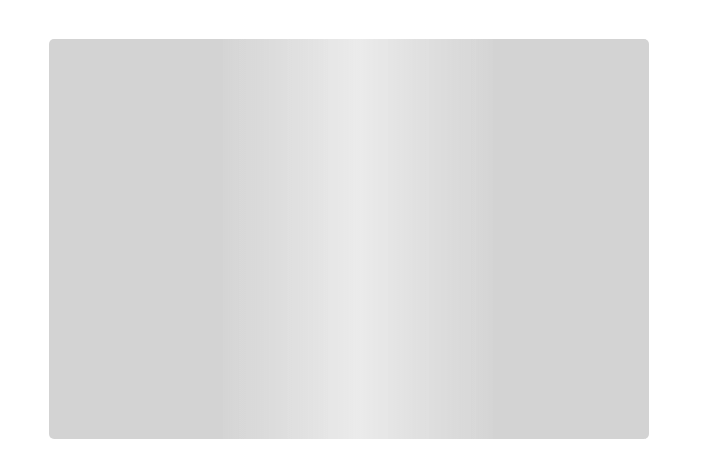
The Top Features to Look for in a Shopfloor Management System
Discover the key features and benefits of implementing a shopfloor management system with Scout Systems. Learn how to boost efficiency and prepare for the future of manufacturing.
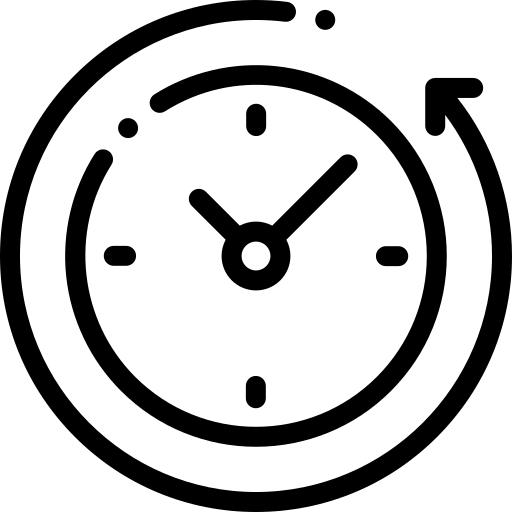

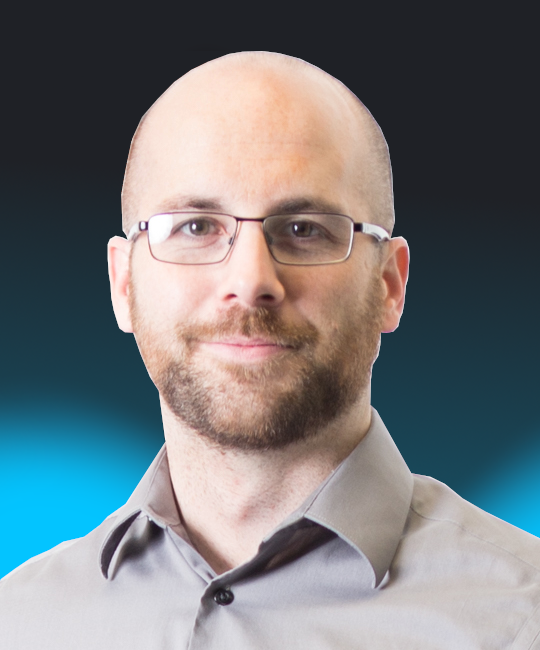
Ben Marsh
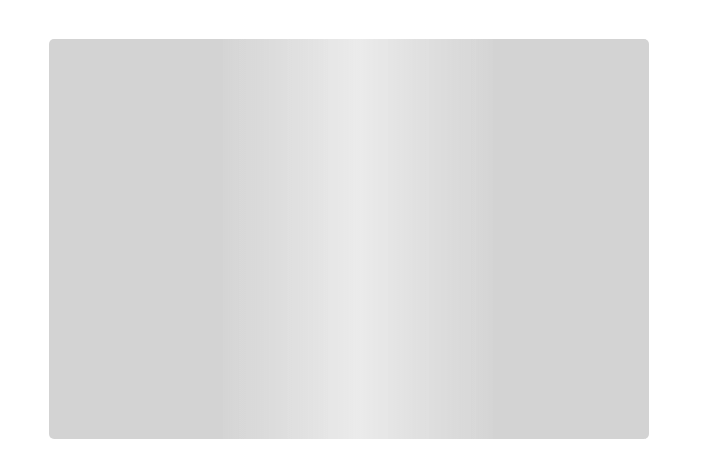
Using Visuals to Simplify Work Instructions
Explore the transformative power of visual work instructions in manufacturing, enhancing clarity, safety, and efficiency on the production floor.
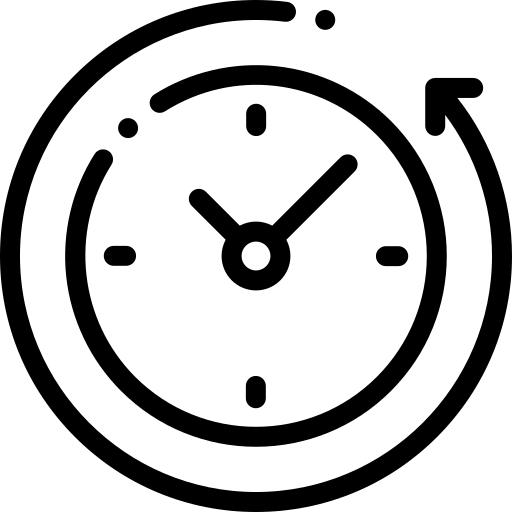

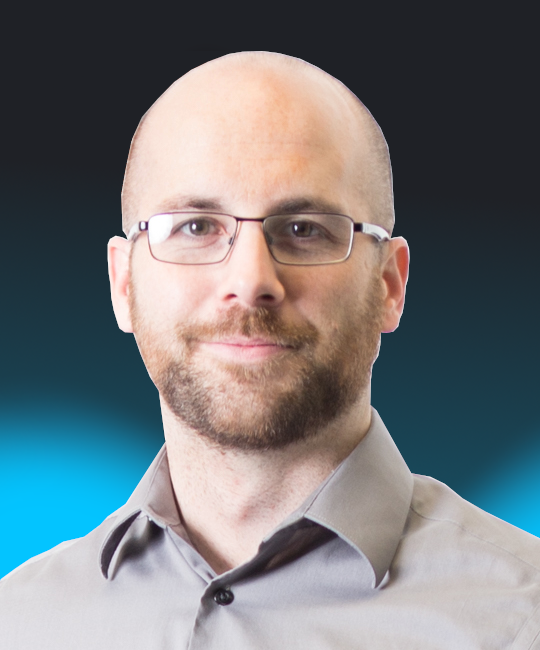
Ben Marsh
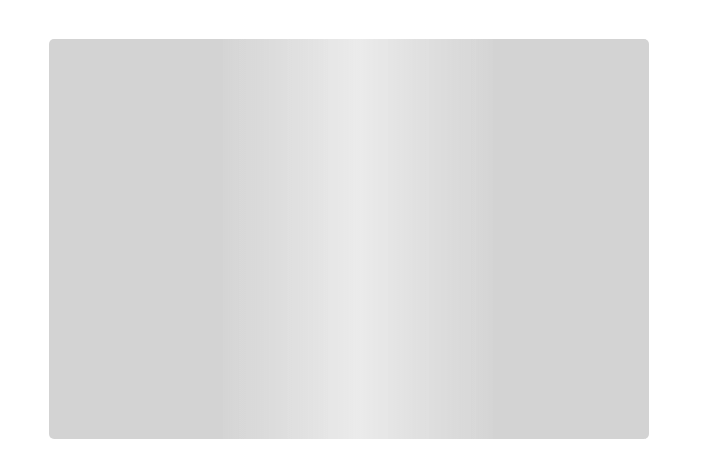
Essential Manufacturing KPIs to Boost Your Production Efficiency
Do you know what manufacturing KPIs are and how they can help your business? Scout Systems is here to share the insights with you.
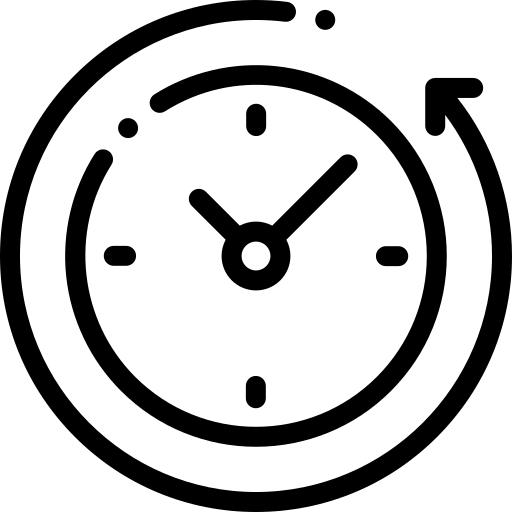

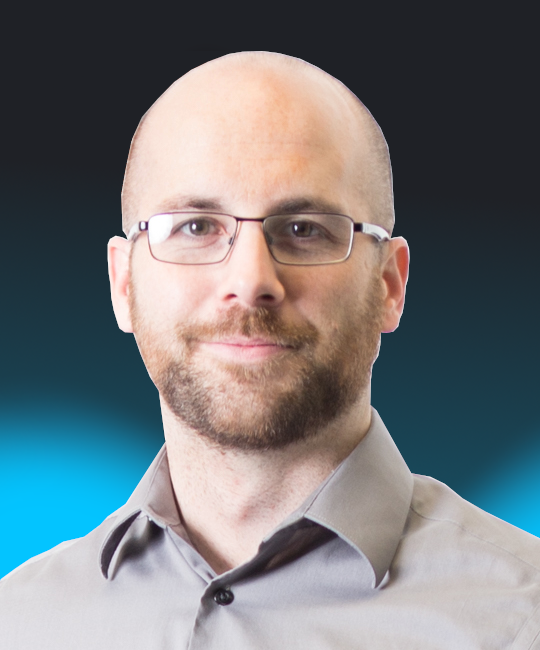
Ben Marsh
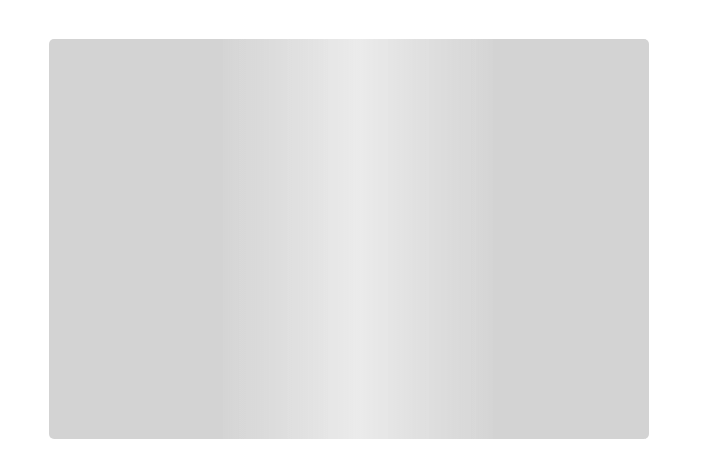
Motivating Operators to use Data Collection Systems
Explore effective strategies for integrating new tech in operations, enhancing team buy-in, and leveraging data for continuous improvement.
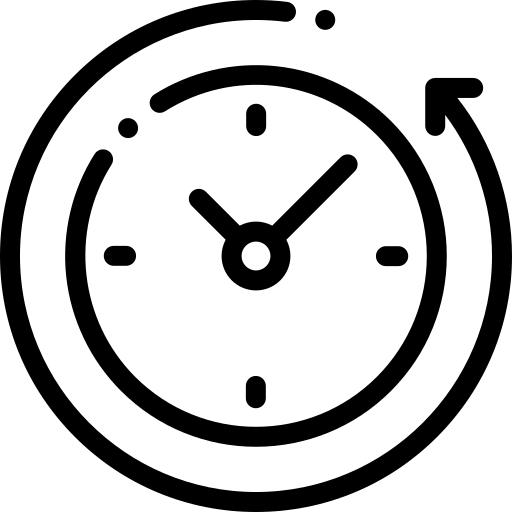

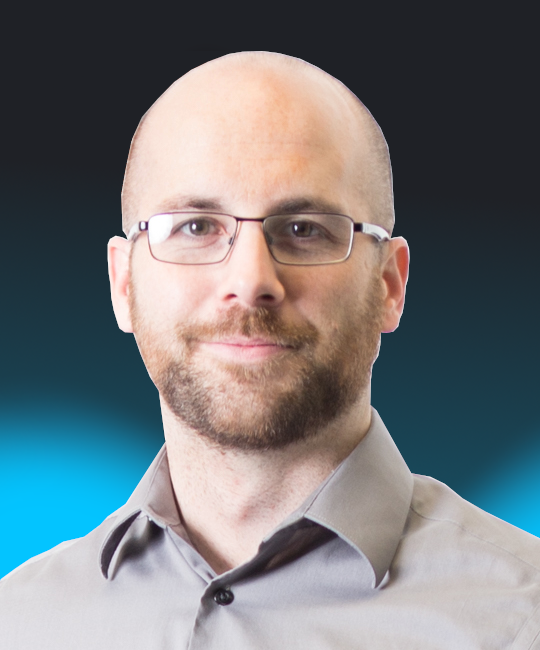
Ben Marsh
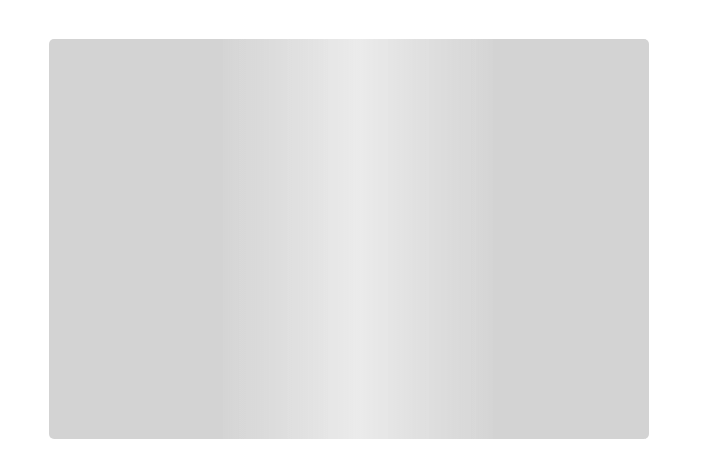
From Paper to Digital: The Evolution of Manufacturing Work Instructions
Transform manufacturing with digital work instructions for enhanced efficiency and quality. Embrace the future with Scout Systems.
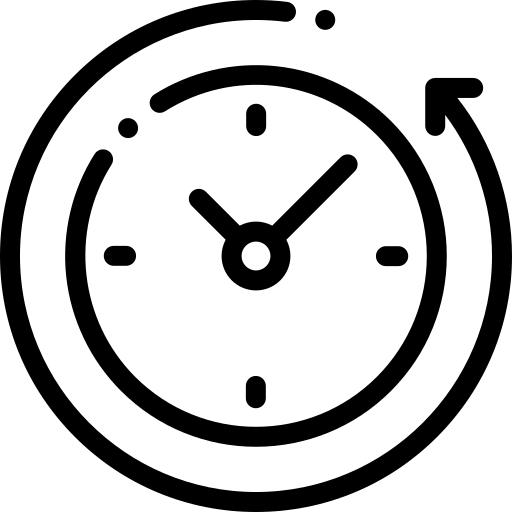

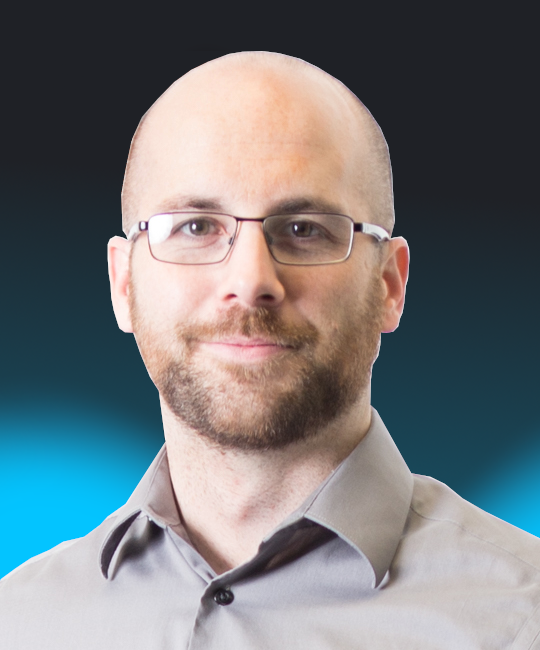
Ben Marsh
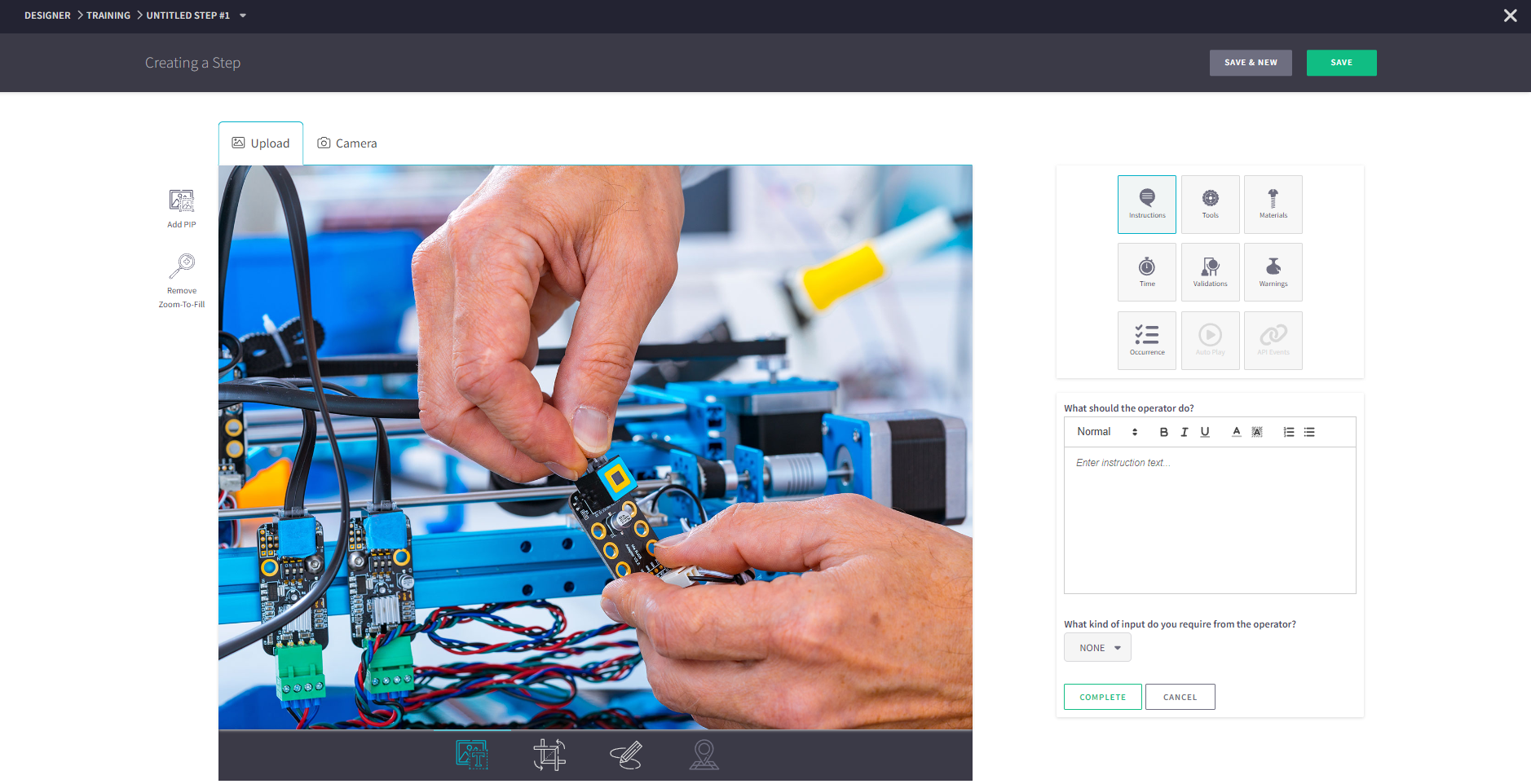
Get Work Instruction Software for Free
Unlock efficiency with Scout Systems' free Work Instruction Software: Perfect for standardizing processes without the hassle. Ready for digital? Switch easily!
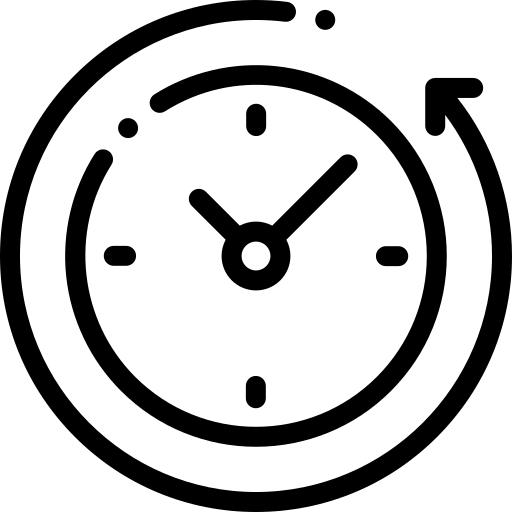

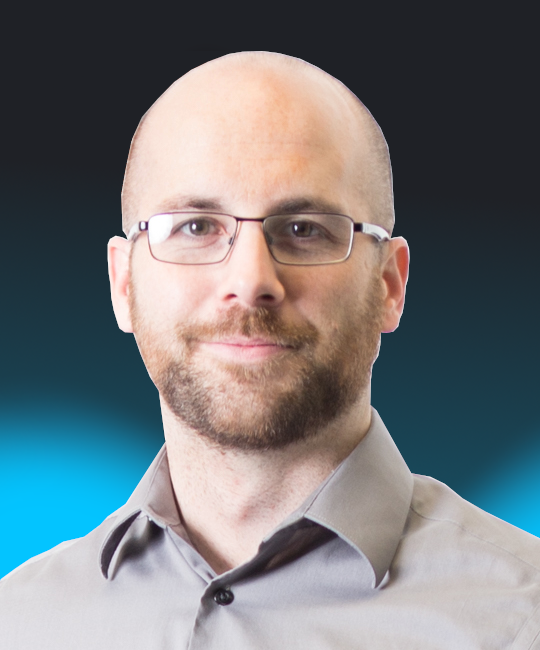
Ben Marsh